This week I was focused on researching and planning next terms practical project. I have decided to improve my previous project, Winston the Robot Dog, where I will be developing more reliable legs and, if I have time, add the ability for him to turn. This will allow me to add onto him yet again next semester, where I will use flex sensors to control him wirelessly with hand gestures. But currently, I am in the phase of researching how I will approach the problem of legs.
It is my understanding that legs in robotics have been a problem for many decades. Both the hardware and software side will pose many issues. The way most modern robots walk is by lifting a leg, and then falling onto it, which is how people walk. This means that I would need to program an inverse kinematics system. An inverse kinematics program would would use point A and B as seperate destinations, and would then calculate the necessary movements to make the leg go there. If this distance is out of reach of the leg, it would get into a position in which it can fall onto the destination. While I get the general logic of an inverse kinematics program, I have researched the practical side of it very little, focussing mainly on the hardware side thus far. While I feel this task is ambitious, I do believe it is possible to achieve next term.
Currently, I have researched the different types of legs used in quadrupedal robots. I found that typically there are three different main types of leg: the prismatic, one which has a single joint at the ‘hip’ and moves from piston extensions. The second type is the articulated leg, where there is both a hip joint and a knee, this is more complex but allows for more precise motion. Finally, there is the redundantly articulated legs. These have a joint at the hip, the knee, and the ankle. This gives similar precision, but more force because of the way it can push off the floor.
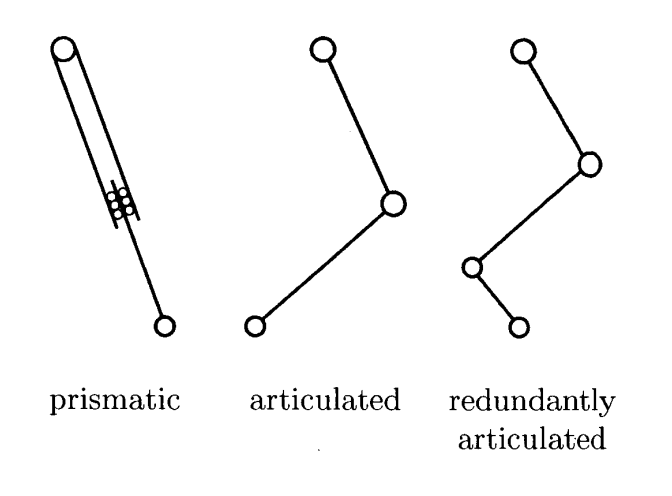
From these, the article I have used goes on to show a design of a redundantly articulated leg. This leg has two possibilities, it can have a motor at the hip and one at the knee, or it can have two motors at the hip. The latter would require me to make tendons for the leg. Tendons would decrease the stress on the legs, and make them have more force. Using two motors at the hip would imply one moves an actuator to control the tendon, thus flexing the knee. The other motor then pivots the entire leg for the knee to re-extend. I will have the ability to apply this to either articulated or redundantly articulated legs simply by adding a bearing at the ankle, connected to the knee by a static tendon. This is the approach I am leaning towards choosing.
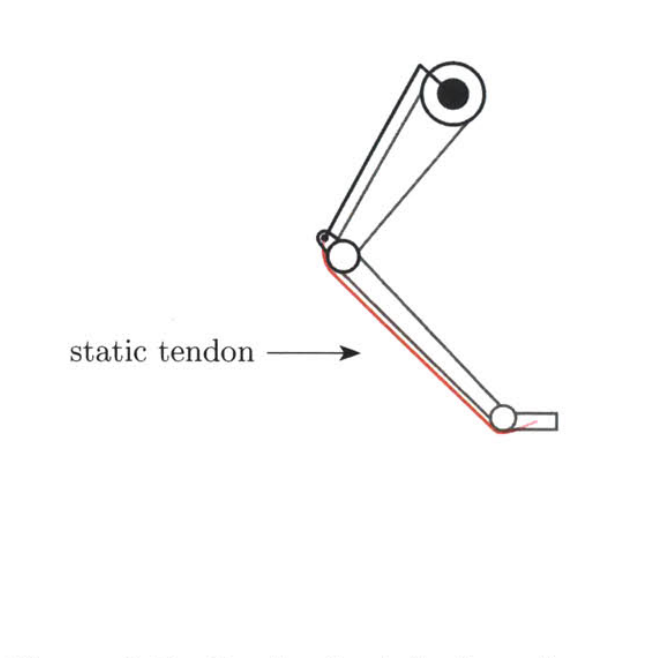
This approach will be difficult, as there will be a lot of work in designing, assembling, and programming even one leg. It is also likely more effective if I make the rear legs different to the front ones, as is with real animals. While I haven’t decided all the details of this yet, I do know that I will have to take my time with the CAD, as last time I got measurements wrong in my rush. I will start developing the legs before the term even begins, probably starting in the next couple of weeks. I feel like this task is going to be very challenging, but also very fun, and I look forward to what I will learn from it.